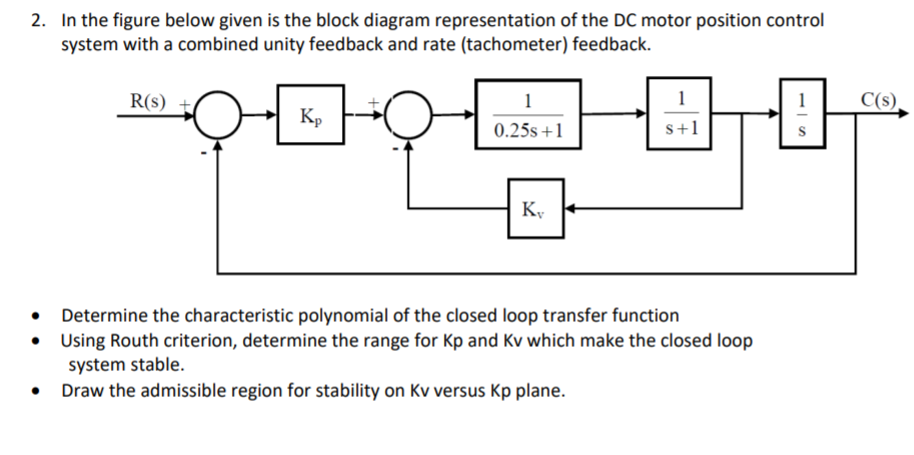
Motor Position Control System. A PWM generator that takes the analog signal that controls the speed of the motor and feeds it to the PWM block in our system. 1 The structure of the control system has the form shown in the figure below. From the main problem the open-loop transfer function of the DC Motor is given as follows. In this post we will see how we can achieve very precise position control of simple DC motor.
A servo motor is a linear or rotary actuator that provides fast precision position control for closed-loop position control applications. P_motor K s Jsb LsRK2. Note that the direction of the motor is already known from the encoder feedback signals from part 1. Such small project are very much fun to do you can learn many concept like PID Close loop system encoder basic by building this project. When full stepping It takes 32 steps for the magnetic rotor inside the motor to complete a full 360 rotation. Position control system is a closed loop control system whose output is the desired angular position of the DC motor.
For this example we will assume the following values for the physical parameters.
Typically conveyor applications operate at either a constant or variable speed requiring only velocity control from a main drive motor. The motor whose position is to be controlled is connected in a closed loop system in which the motor forms the plant. The L290 L291 and L292 together form a complete microprocessor-controlled microcomputer chips DC motor servo positioning system that is both fast and accurate with an adequate software. A servo motor is a linear or rotary actuator that provides fast precision position control for closed-loop position control applications. This motor position control system project aims at building an Arduino PID Proportional derivative and integral calculation-based DC motor Position Control System. These values were derived by experiment from an actual motor in Carnegie Mellons undergraduate controls lab.